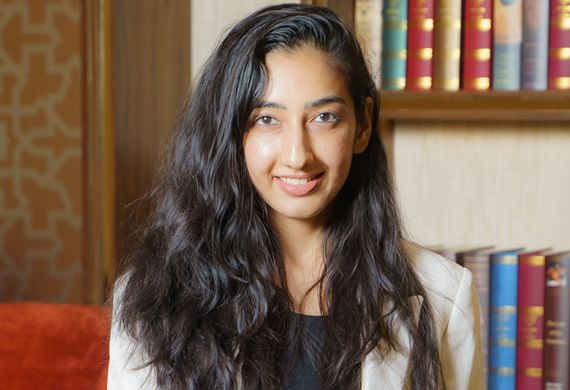
Navigating Change: Leadership in the Time of Disruption
By: Shachi Sharma, Business Head, Henkel
Shachi Sharma is the Business Head of Henkel Adhesive Technologies, a global MNC specializing in adhesives for industrial and B2B consumption. With ten years of experience, Shachi has held various roles, including marketing, digital transformation, and business ownership.
In a conversation with Women Entrepreneurs Review Magazine, Shachi shares her perspectives on the increasing adoption of innovation in the evolving market and how leaders can align digital initiatives with core business functions.
In today's rapidly evolving market, how do you see the general manufacturing and maintenance industry adapting to the digital shift? What trends do you believe will have the most significant impact on shaping the future of the industry?
Customers are becoming increasingly savvy and seeking online solutions for various issues and products. This shift has made it essential for companies to have a presence online, leading customers to the right solutions and making them easily accessible. Digitalization and predictive maintenance are two key trends dominating the market. Digitalization allows customers to easily find the products they need, while predictive maintenance uses data and technology to predict equipment issues. Sustainability is another global trend where . The entire ecosystem, including manufacturing, needs to adopt sustainable methods and align with the circular economy model. Companies are shifting towards high performance, low costs, quality, customized solutions, and localized products.
As industries shift towards more digital and automated processes, what strategies do you think are essential for transforming a traditionally growing business into a future-oriented digital powerhouse? How can industry leaders prioritize digital innovation without compromising core business functions?
To transform a traditional business into a digital powerhouse, it's crucial to upskill teams and view digitalization as an opportunity rather than a threat. Start by investing in robust technological infrastructure and integrating new capabilities to support a digital model. This mindset shift is essential for leveraging digital advancements to your advantage. From a process perspective, invest in the right infrastructure and technology to support this transition. This may involve integrating new technologies, upgrading to big data systems, and potentially acquiring talent from digitally advanced sectors.
Leaders should integrate innovation throughout the organization rather than isolating it in a separate team. Embedding innovation champions across all departments ensures broader acceptance and fosters a culture that embraces change. By aligning digital initiatives with core business functions and engaging the entire organization, you create an environment where innovation is seamlessly adopted and valued.
Disruption often requires leaders to rethink their approaches. How can business leaders in the manufacturing sector cultivate resilience and agility within their teams to navigate uncertainty and drive sustained growth?
For the system to be more resilient and provide adaptability within manufacturing teams, the leadership has to change the mindset of viewing uncertainty and change as threats to opportunities. Developing such a mentality requires questioning the existing practices and being ready to change a typical paradigm. Leaders should positively influence risk-taking and innovation. They should be willing to provide necessary resources, data and infrastructure as well.The constant implementation of new strategies and the promotion of agility enshrine organizations to effectively manage the uncertainties of the market, and consequently, achieve long-term growth. It is therefore essential that the leader leads the process of change, and makes sure that the organization is capable ofhandling future challenges as well as opportunities.
With cross-functional teams playing a pivotal role in driving change, what are some innovative ways to ensure seamless collaboration between diverse functions like sales, marketing, technical, and operations? How can these teams align toward a unified vision of business transformation?
Building a common vision for a business involves welcoming all functions and perspectives, ensuring respect for each, and promoting collaboration across them. This can be achieved through job rotations, allowing employees to move from one function to another, and fostering a sense of unity among different teams. Encouraging these rotations and fostering smaller teams with interlinked targets can also help employees understand their roles and contribute to a more cohesive and effective business. This approach fosters a more inclusive and effective team environment, ultimately leading to increased collaboration and success.
How can leaders in the manufacturing sector ensure that their digital transformation efforts are not just technology-driven but also deeply aligned with the organization's cultural and operational realities, enabling a more sustainable change?
To drive a transformation, align various business functions, and conduct smaller experiments and pilots. Prove results within a smaller team and then apply the success to other functions or groups. Iteratively implement the transformation, showing success in the past. Focus on easier tasks first, such as a specific function or segment, to ensure success. Repeat this model in harder areas. Finally, talk about the change and normalize it by building champions who can reduce resistance and encourage adoption. This approach helps in achieving success and fostering a culture of change.
As you steer your SBU toward a future-oriented organization, what are some of the key indicators you believe industry leaders should track to measure the success of their digital and business transformation initiatives in this evolving market?
Direct metrics are measurable business KPIs that directly benefit the business, such as sales numbers or e-commerce. These metrics help build accountability across functions and measure impact. Quantifiable metrics can make the impact more scalable and make the process more impactful.
Indirect metrics, on the other hand, are softer aspects of change. They involve the shift in mindset of people, as they become more open to change and willing to challenge the business structure. This leads to a more positive attitude towards change and the development of new ideas. Metrics can encourage people to challenge themselves and transform, such as the number of new ideas or segments a team attempts to enter within a specific timeframe.
Message to Readers
The focus on Diversity and Inclusion (DEI) is rapidly changing industries, across all sectors including manufacturing. I would urge the women reading this to not limit themselves, as we can achieve more than we give ourselves credit for. Let’s have big ambitions, challenge ourselves constantly, and create change, one step at a time.